Once all the cloth was cut out, I still had plenty of light and warmth (55 or so) so I decided to crack open the epoxy for the first time (other than a test layup) and get started on the first of many layups. Last weekend I had cut out and setup 3 layers of cloth to fill in the hole where the wood stove chimney used to be here.
I mixed up 2 oz of System Three resin with 1 oz hardener (un-thickened). I have never used System Three in the past, I have always used West System, but I just couldn't justify the huge price difference, and I have heard good things about System Three. An added benefit is the 2:1 ratio which makes for easier math than West's standard 5:1 (not that it's rocket science). Using a 2" chip brush, I put down a coat on the balsa substrate (not core, it is just to hold the laminate in place) and then put the first of 3 layers of glass down. Saturated that with the chip brush and then repeated with the remaining 2 layers of cloth. I left it to cure overnight.
I didn't really have a plan for today when I got up, but it was hard to focus at work and I found myself spending way too much time surfing the web on the Plastic Classic Forum and decided that since the weather was so nice that I should cut out of work early and get a head start on the cabintop layup by getting the balsa glued down in the small sections. Even though these small areas have been a pain because they require a lot more linear area to grind and lots of pieces to cut, they are proving to be a good testing ground for the rest of the project when things get bigger. If I screw up a section, its not the end of the world in terms of cost and work. Plus, whatever I can get done and learn this week will certainly help me go faster and more efficiently when I take next week off.
Anyway, I had everything fairly squared away when I got home from work so I just went to it. First, I filled up a bunch of bags with dirt to use as weights once everything was setup. Next, I mixed up an un-thickened 12 oz batch and wet out the inner skin of each area and the scrim side of each balsa core (scrim side down). At this point I had only used half the batch and had plenty of pot life so I mixed in a cup or so of Aerosil (thixotropic powder) to make it a little thicker than honey and spread it out on the skin of 2 or 3 of the cutout areas and into the corners, then pressed several of the balsa cores in place. Its cool that when the balsa is pressed in place, the thickened epoxy squishes out the sides and fills the gaps between the core and the rest of the deck area.
Mixed up a second 12 oz batch and thickened it up to same consistency and filled in all the gaps of the balsa and any areas I missed along the edges and corners. I also had enough to fill in the areas where hardware will be mounted and all the test holes I had drilled to find the initial bad spots. Not sure if filling the holes was a good idea at this point (especially with Aerosil because it is a structural filler), but what the hell.


At this point it was probably time to stop so I went and had some dinner but while eating I thought about some advice that I had gotten from one of the crew at Plastic Classic Forum. He had said that you can do the whole layup in one shot and avoid the blush removal and sanding to make way for the cloth. He also suggested that you can even mix up the top fairing layer as well, but I figured that was a bit much on the first try and I want to make sure I get the cloth layup correct and want to be able to inspect it once it cures. Basically, with this method you can save a significant amount of time and labor, and I figured that because these small areas are my testing ground, it would be a good place to see if it works.
So after a turkey burger and fries, I went back out and found that the thickened epoxy was hard but tacky
So I pressed in all the inner cloth pieces into place and smoothed them out with my shiny new 3" laminate roller like this. I mixed up a 6 oz batch un-thickened and wet out the first layer of cloth and the tapered edges of the existing glass. Another 6oz batch took care of the outer cloth layer and then used the laminate roller to get any trapped air bubbles out of the layup. I hope at least; the laminate roller seems to work really well, and the cloth makes a satisfying popping sound as the air is forced out of the laminate.
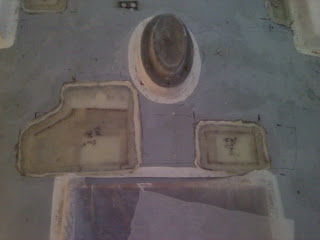
Unless I missed a batch (which is possible), I think I used a total of around 40 oz of epoxy today.
Update: I checked the layup on the way to work this morning having had everything sit overnight for 12 hours and I am really pleased with the outcome. There doesn't appear to be any voids in the layups, and my plastic bag-o-sand weighting technique worked like a dream (sheet of plastic over layup, followed by big loose bag of sand spread evenly over the entire layup).
Matt, am I right that you're wetting out both the inner skin and the core scrim, then applying a layer of thickened epoxy before pressing the core into place? Any guess as to how thick a layer of thickened resin you laid in before the core, to get a proper amount of excess squeezing out into the surrounding gap?
ReplyDelete